The process flow of polyurethane sandwich panel manufacturing:
- rimhydraulic
- Feb 22, 2023
- 1 min read
Preparing the Materials: The process starts by preparing the materials, including the metal sheets for the panel faces, the polyurethane foam, and any additional layers required for specific applications.
Foaming Process: Polyurethane foam is then prepared by mixing polyol and isocyanate in the correct ratio, typically in a mixing head. The resulting mixture is then injected onto the metal sheets as a liquid and expands to fill the space between them.
Facing Attachment: After the foam has expanded, the metal sheets are attached to either side of the foam core, typically with an adhesive layer. Any additional layers, such as a vapor barrier or insulation, can be added at this point.
Curing and Cutting: The sandwich panel is then placed into a curing oven or chamber, where it is heated to the appropriate temperature for the foam to cure and harden. Once the foam has cured, the panel can be cut to the desired size and shape.
Finishing: The final step is to apply any finishing touches, such as painting or laminating, to the panels to prepare them for shipping.
The process flow can vary depending on the specific application and manufacturing method used. However, the general steps of preparing materials, foaming, facing attachment, curing and cutting, and finishing are common to most polyurethane sandwich panel manufacturing processes.
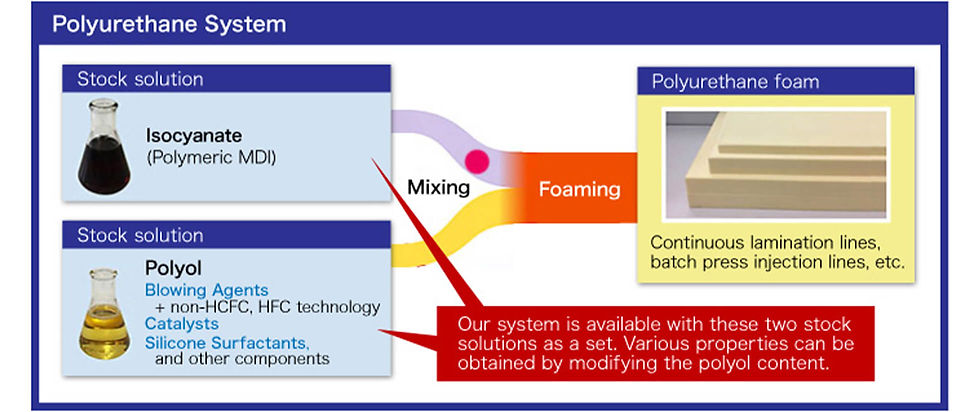
Comments